A valve actuator is a mechanical device that controls the opening and closing of a valve. It is typically used in industrial applications such as pipelines, chemical plants, and refineries where precise control of fluid flow is critical. Actuators are an essential part of many industrial processes as they provide automatic control of fluid flow.
A valve actuator plays a critical role in ensuring the efficient and reliable operation of the system. It can be either electric, hydraulic, or pneumatic. A valve actuator can be controlled by a variety of signals, including manual switches, sensors, and programmable logic controllers (PLCs).
The main purpose of a valve actuator
The main purpose of a valve actuator is to control the flow of fluids such as liquids or gasses through a pipeline or other industrial process. When a valve is open, fluid can flow through; when it is closed, flow is prevented. The valve actuator controls the position of the valve, which determines whether fluid can flow through the valve. Thus, the function of a valve actuator is to convert energy into motion to operate a valve.
Valve actuators come in many different shapes and sizes. An actuator can be operated manually, electric, pneumatic, or hydraulic. As the name implies, manual actuators are the simplest type and are hand-operated. In contrast, electric actuators use an electric motor to operate the valve. Pneumatic actuators use compressed air to move the valve, and hydraulic actuators use pressurized fluid to do the same.
How does a Valve Actuator Work?
Regardless of the type of actuator, the basic function remains the same. The actuator converts an input signal into a mechanical motion that is then used to open or close the valve. The input signal can be in the form of an electric current, pneumatic pressure, or hydraulic pressure, depending on which type of actuator is used.
What is the working principle of the valve actuator?
Valve actuators function by converting energy from a power source into mechanical energy that is used to move the valve stem. This conversion is achieved through a series of components, including a motor or other power source, a gearbox or transmission, and a mechanism for converting the rotary motion of the motor into linear motion. In some designs, the actuator includes a feedback mechanism, such as a position sensor or limit switch. This feedback mechanism provides information about the position of the valve.
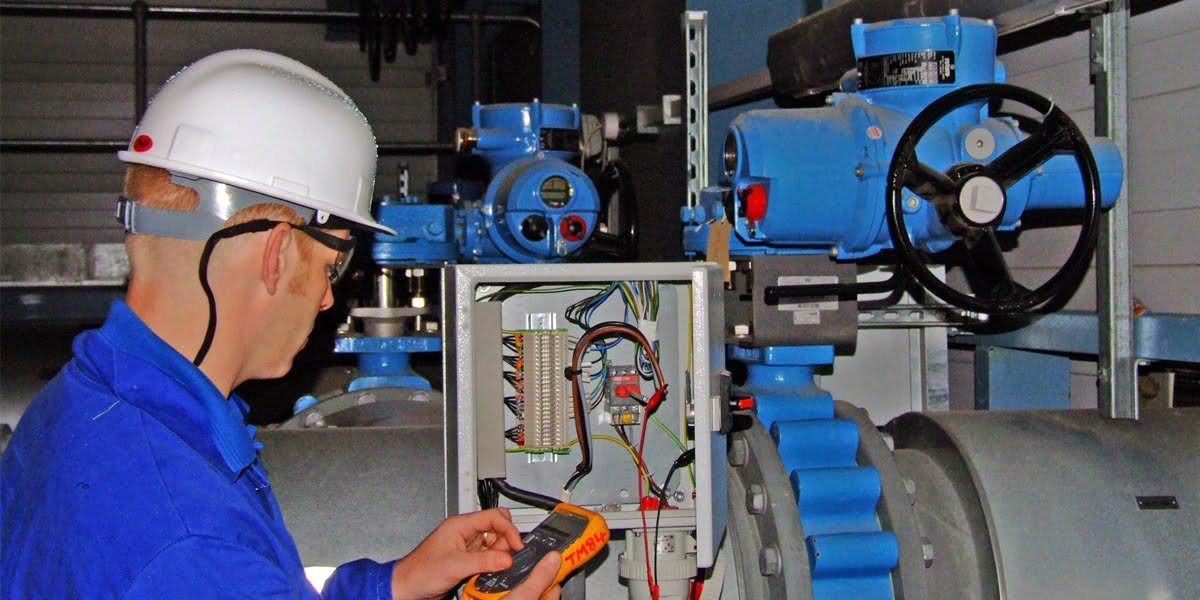
The main reason for needing a valve actuator
One of the main advantages of using a valve actuator is that it allows precise control of fluid flow. By adjusting the position of the valve, the flow rate of the fluid can be regulated to meet specific requirements. Flow rate requirement is particularly important in industrial applications where the flow rate of a fluid can significantly affect the efficiency of the process.
Valve actuators also provide a high level of reliability and safety. Because they are mechanical devices, they are less prone to failure than other types of control systems, such as electronic control systems. In addition, valve actuators can be designed to operate in hazardous environments, such as those with high temperatures or corrosive chemicals.
What are the 4 types of valve actuators?
There are several types of valve actuators, each with its advantages and disadvantages. Some of the most common types are:
Manual actuators
These are the simplest type of actuator and are operated by hand. Manual actuators are often used in small-scale applications where precise control is not required. These actuators require manual operation, such as turning a handwheel or lever. Manual actuators are typically less expensive than powered actuators but require constant monitoring and can be time-consuming to operate.
Electrical actuators
These valve actuators use an electric motor to open and close the valve. They are commonly used in applications that require precise control and where the valve needs to be operated remotely.
Valve actuators are ideal for applications requiring precise control and easily integrated into automation systems. They are also relatively quiet and require minimal maintenance.

Pneumatic actuators
These actuators use compressed air to move the valve. Pneumatic actuators are often used in applications with a ready supply of compressed air and where fast response times are required. These actuators use compressed air or gas to drive the valve stem. Pneumatic actuators are typically less expensive than electric actuators and well-suited to high-pressure applications. However, they can be noisy and require a source of compressed air.
Hydraulic actuators
These actuators use pressurized fluid to move the valve. Hydraulic actuators are often used where high force is required, and precise control is needed. These actuators use hydraulic pressure to drive the valve stem. Hydraulic actuators are ideal for applications requiring high force or speed. They can be used in environments with high temperatures or corrosive materials. However, hydraulic actuators can be expensive and require regular maintenance.
Actuator classification according to motion types
Valve actuators can also be classified based on the type of motion they provide. The two most common types of motion are rotary and linear.
Rotary valve actuator
Rotary valve actuators provide rotary motion and are used to control ball valves and butterfly valves. They can be electrically, hydraulically, or pneumatically operated. They are often used in applications requiring high precision.
Linear valve actuator
Linear actuators for valves provide linear motion and are used to control gate valves and globe valves. They can be electrically, hydraulically, or pneumatically operated. They are often used in applications requiring a high amount of force to operate the valve.
Special Actuators
In addition to these types, specialized actuators are available for specific applications. For example, explosion-proof actuators are designed to operate in hazardous environments, while high-temperature actuators can withstand extreme temperatures.
Conclusion on actuators
Valve actuators are an essential part of any valve system as they allow remote control and operation of the valve. They come in a variety of designs and are electrically, hydraulically, or pneumatically operated. Valve actuators are used in various applications in different industries, including water treatment, oil and gas, chemical processing, HVAC, and power generation. Choosing the right valve actuator type depends on the specific application and performance requirements