The advent of automation has ushered in a new era of efficiency in industrial operations. At the forefront of this automation revolution is modulating actuators – indispensable components of valve automation systems in a range of sectors, including but not limited to petrochemicals, oil and gas, and water treatment. This comprehensive guide aims to provide an in-depth exploration of the multifaceted world of modulating actuators, covering their functions, types, and applications. By delving into the intricacies of these vital devices, this guide will equip you with the knowledge necessary to navigate the complex landscape of industrial automation.
What is a modulating actuator?
In industrial processes, the flow rate of fluids is of utmost importance. To achieve this, a modulating actuator is used as it allows the control of fluid flow by adjusting the valve position. It’s an electro-mechanical device that can precisely modulate the flow of fluids. These actuators are designed to meet the high demands of accuracy and reliability required in various industrial applications such as chemical, petrochemical, and water treatment plants.
Modulating actuators ensure that the fluid flow is optimally controlled, making them ideal for use in industries where precise flow control is critical to the process. With their advanced control features and ability to handle high-pressure conditions, modulating actuators are essential to valve automation systems.
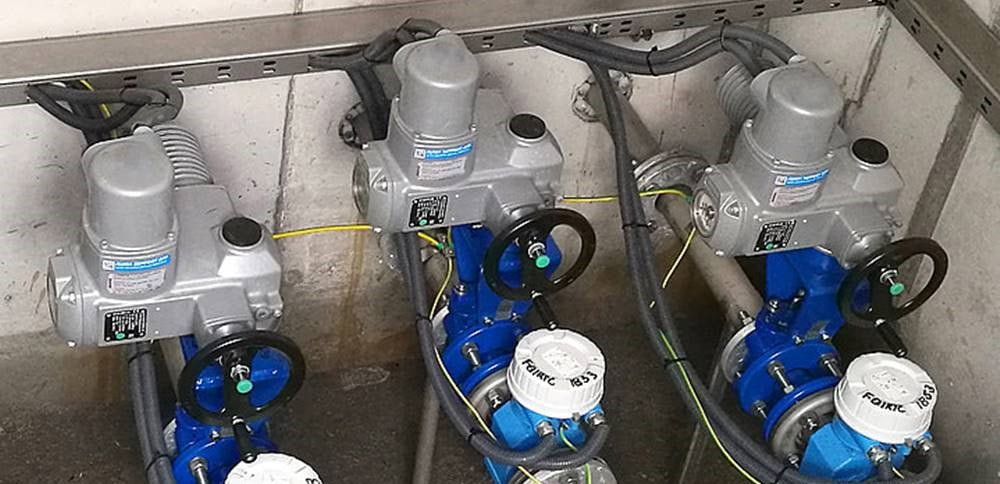
Functions of modulating actuators
Modulating actuators perform various functions in different industrial applications, including:
- Control Flow Rate: A modulating actuator is used to control the flow rate of fluids in industrial processes.
- Precise Flow Control: The actuator provides precise flow control, ensuring that the right amount of fluid is delivered at the right time.
- Automatic Control: Modulating actuators are designed to operate automatically, making them ideal for remote control applications.
- Control Pressure: The actuator can also be used to control pressure in pipelines and valves.
Applications of modulating actuators
Modulating actuators are used in a wide range of industrial applications, including:
- Oil and Gas: In the oil and gas industry, modulating actuators are used to control the flow of oil and gas through pipelines.
- Petrochemical: Modulating actuators are used to control the flow of chemicals in petrochemical plants.
- Water Treatment: Modulating actuators are used to control the flow of water in water treatment plants.
- Power Generation: Modulating actuators are used to control the flow of steam in power generation plants.
Types of modulating actuators
There are two main types of modulating actuators:
- Pneumatic Modulating Actuators: These actuators use compressed air to operate the valve. They are often used in hazardous environments where electrical equipment is not permitted.
- Electric Modulating Actuators: These actuators use electric power to operate the valve. They are often used in applications where precise control is required.
Applications of modulating actuators
Modulating actuators are used in a wide range of industrial applications, including:
- Oil and Gas: In the oil and gas industry, modulating actuators are used to control the flow of oil and gas through pipelines.
- Petrochemical: Modulating actuators are used to control the flow of chemicals in petrochemical plants.
- Water Treatment: Modulating actuators are used to control the flow of water in water treatment plants.
- Power Generation: Modulating actuators are used to control the flow of steam in power generation plants.
How to choose the right modulating actuator
When selecting a modulating actuator, there are several factors to consider, including:
- Type of Fluid: The type of fluid being controlled will determine the type of actuator needed.
- Flow Rate: The required flow rate will determine the size of the actuator needed.
- Operating Environment: The operating environment will determine the type of actuator needed. For example, in hazardous environments, a pneumatic actuator may be required.
- Control Accuracy: The required control accuracy will determine the type of actuator needed.
- Maintenance Requirements: The maintenance requirements will determine the type of actuator needed. For example, electric actuators may require more maintenance than pneumatic actuators.
Advantages of modulating actuators
Modulating actuators offer several advantages over traditional actuators, including:
- Precise Control: Modulating actuators provide precise control of fluid flow, ensuring that the right amount of fluid is delivered at the right time.
- Automatic Operation: Modulating actuators can operate automatically, making them ideal for remote control applications.
- Energy Efficiency: Modulating actuators are more energy-efficient than traditional actuators, reducing energy consumption and operating costs.
- Reduced Maintenance: Modulating actuators require less maintenance than traditional actuators, reducing downtime and maintenance costs.
FAQs
Q: What is the difference between a modulating actuator and a traditional actuator?
A: A traditional actuator operates in an on-off mode, while a modulating actuator provides precise control of fluid flow.
Q: What type of actuator should I choose for my application?
A: The type of actuator needed will depend on several factors, including the type of fluid being controlled, the required flow rate, the operating environment, the required control accuracy, and the maintenance requirements.
Q: Can modulating actuators be used in hazardous environments?
A: Yes, pneumatic modulating actuators are often used in hazardous environments where electrical equipment is not permitted.
Conclusion
Modulating actuators are an indispensable part of automation systems across various industrial applications. As they are responsible for precisely controlling fluid flow, it is essential to choose the right actuator to ensure the optimal functioning of industrial processes. The selection process considers several key factors, including the fluid type and flow rate, the operating environment, control accuracy required, and maintenance requirements.
With the right modulating actuator in place, industries can expect improved efficiency and performance, enabling them to meet their production goals more efficiently. By choosing the appropriate actuator for their unique needs, industrial operators can ensure the accurate and reliable control of fluid flow in their systems.